Bentley and Siemens recently briefed ARC Advisory Group about their vision for an open, cloud-based solution for engineering and operations. The cloud solution – a portal accessed through a browser – will federate data sources, provide functionalities and facilitate the management of the digital twin of the asset, throughout its life cycle. It would overcome the current challenge of engineering tools that are poorly connected to asset information during operation and vice versa, as well as the disconnect between functional (1D and 2D) and spatial (3D) information.
The solution would also provide compliance management in a single environment. The solution would facilitate the construction of digital twins as a federation of data from many on-line and off-line sources and require very little IT integration. It would help incorporate data from digitally inaccessible sources, sometimes referred to as “dark data”, and mobile sources used in the field.
An accurate, up-to-date accessible digital twin reduces time to operational readiness and can influence time to market. The ease with which this twin can be updated during operation or modified during projects, supports the need for increased flexibility and adaptability. The seamless and on-going integration of process engineering, maintenance, 3D representation and operational performance information, speeds up and supports continuous improvement and thereby efficiency, sustainability and return on assets. Owner-operators can combine the solution with asset management best practices to improve useful life and asset value.
The digital twin makes it easier to engineer for safety and compliance and verify compliance of the asbuilt and as-maintained facility. Different types of cloud services, including on-premise and hybrid, will be possible. Pure cloud and hybrid implementations allow easy scalability and reduce bottlenecks that potentially occur when users simultaneously access a database. The solution will be implemented as microservices, a suite of independently deployable modular services that can be complemented and the roadmap of which can be adapted based on client needs.
Challenges in Capital Projects in the Process Industries
The financial crisis of 2007-2008 and the recent drop in oil prices that led to significant reductions in demand and asset utilization has created the awareness that large-scale and single-purpose assets can have important drawbacks when markets are highly volatile. The resulting pressure to increase efficiency and return on assets requires shorter times to operational readiness and greater flexibility in operating and modifying assets to follow market demand. In practical terms:
- For plants under construction by engineering procurement and construction firms (EPC’s), owner-operators (OO’s) require tighter collaboration than before. Examples of these requirements are electronic design reviews and tracking of construction and commissioning progress against electronic documents and 3D surveys.
- The asset information built up during engineering and construction is often incomplete or outdated at the moment of transfer. NIST estimates the cost of information losses during handover to be 1.8% of capital expenditures. There is a huge opportunity to enhance the process by improving change management to ensure the data is accurate and information is reused.
- When engineering or maintenance trouble shoot an operational issue or need to start a modification project, they lose precious time when trying to determine the current status and performance of the asset before starting their actual work because often, the asset information is missing or inaccurate. Functional, operational and 3D spatial information – for the plant, building, or both - are often not available side by side and are often inconsistent. Furthermore, time is often lost due to inaccurate information on spare parts. NIST estimates the cost of information losses in the operate-maintain phases of the asset to be 2.4% of the capital expenditure cost. Complete, accessible, and accurate asset information has the potential to shorten project duration and “mean time to repair” (MTTR), and to lower operational and capital expenditures.
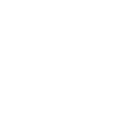
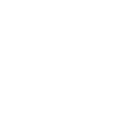
- High reliability is required for the best return on assets and process safety. Reliability-centered maintenance methodologies are well advanced and remote equipment monitoring is available. To be efficient, reliability engineers need seamless access to all asset information.
- As regulatory requirements tighten, compliance costs increase. In some cases, compliance becomes impossible as accurate information cannot be produced at any point in time. The efficiency of compliance processes must be improved using electronic design and requirement documentation, with electronic sign-offs.
- In the foreseeable future, modular production plants will be built that are easier to modify and use more energy and material efficient process technologies. Initial use in pilot installations will gradually be extended to industrial production. This will further increase the pressure on flexibility and efficiency for fast-track engineering as well as on operation and requirements for a digital twin.
Todays’ tools are often specialized for a certain type of task but lack the connectivity that would enable the easy comparison and cross-referencing of asset information. Engineering tools are well suited for design and build phases but may be less suited for use in operations and maintenance. In most instances, the functional information in those tools is disconnected from 3D designs, even though the designs could provide excellent context for operations training, maintenance task planning, trouble shooting, and decision making under abnormal conditions.
In turn, 3D designs for project planning lack access to engineering design or information, and/or maintenance records, thus narrowing the user’s view. In fact, 3D models are rarely updated after plant changes, and are typically not reused for operator training. One of the reasons for the disconnect between simulations and asset information is the lack of support for keeping them in synch. The tools used are often demanding on skills, license costs, computing and network resources, and this demand fluctuates wildly. When a project is executed, the bottlenecks appear.
As most plants in areas with advanced economies are brownfield plants which were built decades ago, asset documentation is a real challenge. While there is a business case for up-to-date asset information, ARC estimates that the average percentage of assets with current asset information is most likely below 50 percent and rarely exceeds 70 percent. It is troublesome that most owner-operators are not able to identify their out-of-date information, let alone show a progression of improvement over time. When users are aware that some available data is incomplete, inaccurate, or outdated, they understandably begin to question the validity of all accessible data.
Technology trends and vision
Todays’ cloud and virtualization technologies enable an easy and instantaneous on-demand availability of computational resources and services. On premise clouds would limit a company to their own infrastructure, but hybrid private/public cloud solutions enable the on-demand extension of cloud-based resources. This flexibility enables responsive, collaborative engineering and asset management with its highly variable demand on resources.
Cloud platforms can be configured for high availability and provide close to real-time updates of information upon entry by the user. Security risks of cloud solutions are a concern but can be managed to a level of acceptable residual risk with appropriate measures. Cloud platforms and software as a service (PaaS and SaaS) have introduced the concept of services, such as analytics, that the user can apply to his or her data, to study correlations or cause-and-effect relationships, thereby providing a significant improvement in productivity.
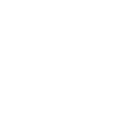
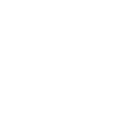
The industrial IoT provides the possibility to monitor plant or equipment performance remotely. This domain is advancing in great strides, with secure and standardized connectivity lowering the cost and effort of developing applications and providing process and maintenance engineers with more opportunities for analytics.
The Vision
Combining these technology trends with deep domain knowledge and the existing challenges discussed above, Bentley and Siemens developed a vision for an open, cloud-based solution for engineering and operations. The cloud solution – accessed through a browser – will federate data sources, provide functionalities in the form of microservices, and facilitate the management of the digital twin of the asset, throughout its life cycle. The solution will use state-of-the-art cyber security, information segmentation related to user roles and role-based access, management of change, and data traceability and visualization.
Data sources and data access
The solution would facilitate the construction of the digital twin as a federation of data from many sources. This can include engineering databases, maintenance repositories, stored 3D models, 3D surveys, and photogrammetric information. Access to schedule, cost and other information accessible through ERP, recipe databases, project and portfolio management systems, LIMS and more would be provided via connectors. This approach of distributed data management, where every data point is interconnected, avoids replication, while providing consistency and accessibility. The data will be distributed through cloud services, as hybrid or on-premise instances, and utilize the users’ local storage.
The process would require very little IT integration. In addition to information accessible on-line, there is a category of inaccessible sources, such as PDF documents, drawings or paper documents, and electronic data in legacy systems that can benefit a broader set of users, when made available. The portal would include intelligent services to help incorporate, analyze and connect data from these sources, also called “dark data.”
Functionalities to access this data would include smart scanning to interpret schematics and drawings, reading from instrumentation and equipment lists, and linking diagrams with data objects describing the physical objects. Other software components would help extract locked data and making it available to those who may need it.
As the data quality may be inconsistent, validation steps will allow the differentiation of useful data from poor data. Upon validation, the data can be linked to plant and data objects. In addition, the solution provides the possibility to add untagged plant information on field on his or her mobile device. These functionalities add context to “dumb data” and can considerably reduce the effort of building the digital twin and increase the percentage of documented asset information.
The solution will also provide separate views and environments to manage a plant in operation and projects on brownfield operations. It will separate data related to the project from characteristics, history, and records related to the operating asset.
The solution will provide capabilities for users to work off-line based on snapshots of asset information recorded at any point in time, with the possibility of subsequent updates synchronized on demand. As a digital twin of the physical plant, asset information changes over time, and it can be important to compare the asset states at different points in time or to analyze its evolution. Therefore, the solution will provide the capability to ”travel” through the digital asset history. The solution will help users maintain process simulations throughout the asset lifecycle, by providing the capability to associate a simulation with an asset information snapshot, for example at handover (as-built), and at every major plant modification.
ARC Advisory Group
www.arcweb.com